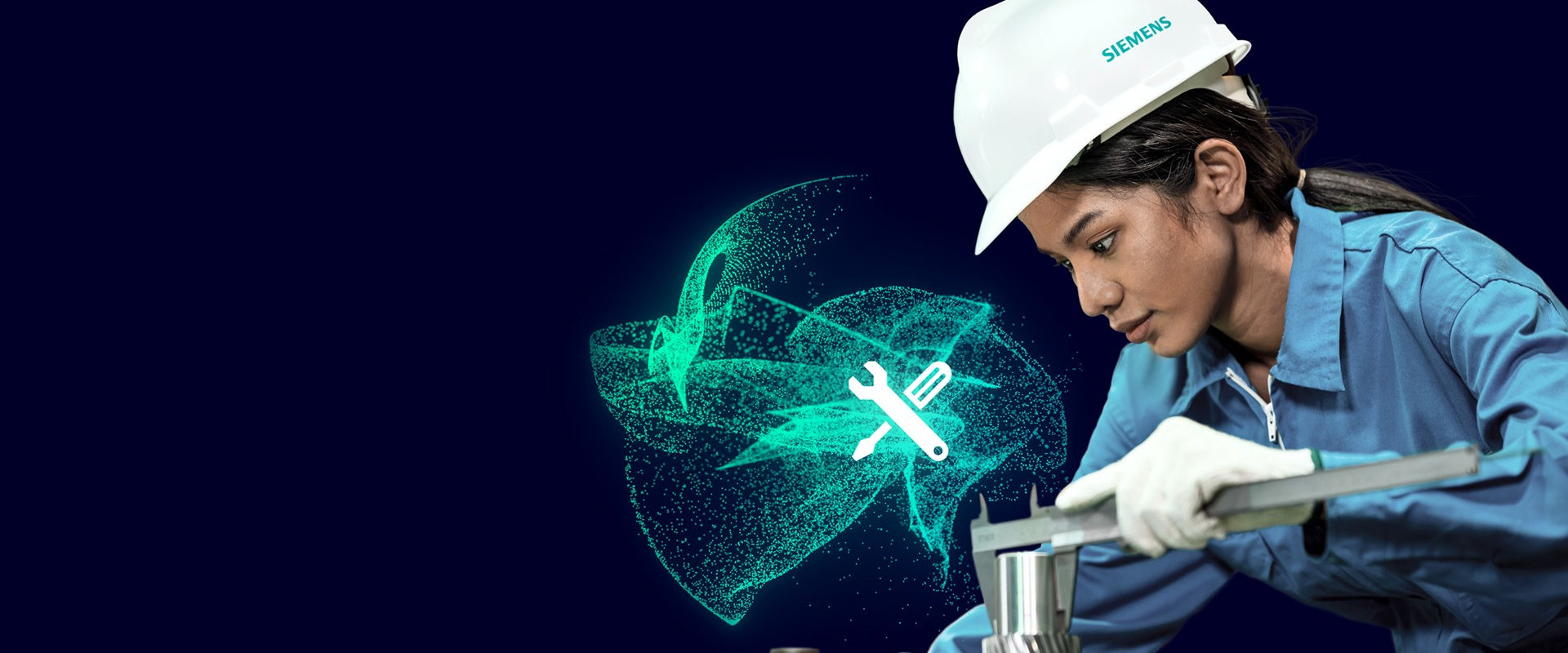
In the world of machinery, equipment, and property management, two terms often come up: repair and maintenance. While these terms are sometimes used interchangeably, they represent distinct activities with different objectives, costs, and impacts on the longevity and performance of assets. Understanding the difference between repair and maintenance is crucial for businesses, homeowners, and maintenance professionals alike. This article will delve into the nuances of repair and maintenance, their relationship, and how they impact asset management, operational efficiency, and financial planning.
What is Maintenance?
Maintenance refers to the proactive measures taken to keep equipment, machinery, or systems in optimal working condition. The primary goal of maintenance is to prevent wear and tear, avoid unexpected breakdowns, and extend the lifespan of assets. Maintenance is typically planned and scheduled, ensuring that systems operate efficiently and reliably over time.
Types of Maintenance
- Preventive Maintenance (PM): Regularly scheduled tasks aimed at preventing equipment failure. Examples include oil changes, filter replacements, and routine inspections.
- Predictive Maintenance: Uses data and monitoring tools to predict when maintenance should be performed based on the condition of the equipment.
- Corrective Maintenance: Addresses minor issues before they escalate into major problems. This is often a bridge between preventive and repair activities.
- Reliability-Centered Maintenance (RCM): Focuses on maintaining system functionality by identifying and addressing potential failure points.
Common Maintenance Activities
- Inspections and Cleaning: Regularly checking components for signs of wear and keeping them free of dirt and debris.
- Lubrication and Adjustments: Ensuring moving parts are well-lubricated and properly adjusted for optimal performance.
- Replacing Consumables: Swapping out parts like belts, filters, and fluids that degrade over time.
- System Upgrades: Installing new components or software to improve performance and efficiency.
For example, in an automotive context, maintenance includes oil changes, tire rotations, and brake inspections. For HVAC systems, it involves cleaning coils, checking refrigerant levels, and inspecting ductwork.
What is Repair?
Repair, on the other hand, is a reactive process that involves fixing or replacing components that have failed or are no longer functioning correctly. Repairs are typically unplanned and occur in response to a breakdown or malfunction. They are often more costly and time-consuming than maintenance because they address issues after they have already caused disruption.
Read other article: what to do when your aircons starts blinking
Types of Repairs
- Emergency Repairs: Immediate fixes required to restore functionality after a sudden breakdown.
- Partial Repairs: Addressing issues that affect performance but do not completely halt operations. For example, a vehicle with a dirty air filter may still run but with reduced efficiency.
- Complete Repairs: Fixing failures that render an asset unusable, such as replacing a broken engine or a malfunctioning compressor.
Common Repair Activities
- Troubleshooting: Identifying the root cause of a problem.
- Component Replacement: Swapping out damaged or worn-out parts.
- System Restoration: Bringing equipment back to its original working condition.
For instance, repairing a car might involve replacing a blown head gasket or fixing a damaged transmission. In a home setting, repairs could include fixing a leaking roof or replacing a faulty furnace.
Key Differences Between Repair and Maintenance
Aspect | Maintenance | Repair |
---|---|---|
Nature | Proactive | Reactive |
Cost | Generally lower | Often higher |
Frequency | Scheduled and regular | As-needed, often unexpected |
Downtime | Minimal, planned | Significant, unplanned |
Goal | Prevent issues and extend asset life | Restore functionality after failure |
Impact on Longevity | Enhances lifespan | May indicate neglect if frequent |
The Relationship Between Repair and Maintenance
While repair and maintenance are distinct, they are closely interconnected. A well-executed maintenance program can significantly reduce the need for repairs by identifying and addressing potential issues before they escalate. Conversely, neglecting maintenance often leads to more frequent and costly repairs, increased downtime, and even premature asset failure.
For example:
- Regular maintenance on a vehicle, such as oil changes and brake inspections, can prevent engine failure or brake system malfunctions.
- In an industrial setting, predictive maintenance can identify wear and tear on machinery components, allowing for timely replacements before a breakdown occurs.
Financial and Operational Implications
Cost Management
- Maintenance Costs: These are predictable and can be budgeted for. While they require an upfront investment, they save money in the long run by preventing costly repairs.
- Repair Costs: These are often unpredictable and can be significantly higher, especially if emergency services or major component replacements are required.
Downtime and Productivity
- Maintenance: Scheduled maintenance minimizes unplanned downtime, ensuring continuous operations and productivity.
- Repairs: Unexpected breakdowns can lead to significant downtime, disrupting workflows and causing delays.
Asset Longevity
- Maintenance: Regular upkeep extends the lifespan of assets, maximizing their return on investment.
- Repairs: Frequent repairs may indicate poor maintenance practices and can shorten the lifespan of equipment.
Repair and Maintenance in Different Contexts
Automotive Industry
- Maintenance: Oil changes, tire rotations, brake inspections.
- Repair: Engine overhauls, transmission replacements, fixing electrical issues.
Residential Property
- Maintenance: HVAC system cleaning, gutter cleaning, roof inspections.
- Repair: Fixing leaks, replacing broken appliances, repairing structural damage.
Industrial and Manufacturing
- Maintenance: Lubricating machinery, replacing worn-out parts, conducting safety inspections.
- Repair: Restoring production lines after a breakdown, replacing faulty equipment.
Tax and Accounting Considerations
MRO (Maintenance, Repair, and Operations)
Businesses can deduct routine maintenance and repair expenses from their taxes. However, expenses related to improvements, restorations, or adaptations must be capitalized rather than deducted.
Capital Expenses vs. Operating Expenses
- Maintenance and Repairs: Typically classified as operating expenses.
- Improvements and Upgrades: Considered capital expenses and must be depreciated over time.
Best Practices for Effective Maintenance and Repair Management
- Adopt a Proactive Approach: Focus on preventive and predictive maintenance to minimize the need for repairs.
- Leverage Technology: Use Computerized Maintenance Management Systems (CMMS) like MaintainX to automate scheduling, track asset performance, and manage inventory.
- Train Staff: Ensure maintenance teams are well-trained to handle both routine tasks and unexpected repairs.
- Monitor and Analyze Data: Use data from condition-monitoring tools to identify trends and address potential issues early.
- Balance Resources: Allocate 80% of resources to proactive maintenance and 20% to corrective repairs for optimal cost-effectiveness.
Conclusion
Understanding the difference between repair and maintenance is essential for effective asset management. While maintenance is a proactive strategy aimed at preserving functionality and extending asset life, repair is a reactive response to restore functionality after a failure. By prioritizing maintenance, businesses and individuals can reduce repair costs, minimize downtime, and maximize the lifespan of their assets. Whether you’re managing a fleet of vehicles, maintaining a home, or overseeing industrial machinery, a balanced approach to repair and maintenance is key to achieving long-term success.
By implementing best practices and leveraging modern tools, you can ensure that your assets remain in peak condition, saving time, money, and resources in the long run. Remember, prevention is always better than cure.